How breweries can streamline project management with the help of process engineering consultants
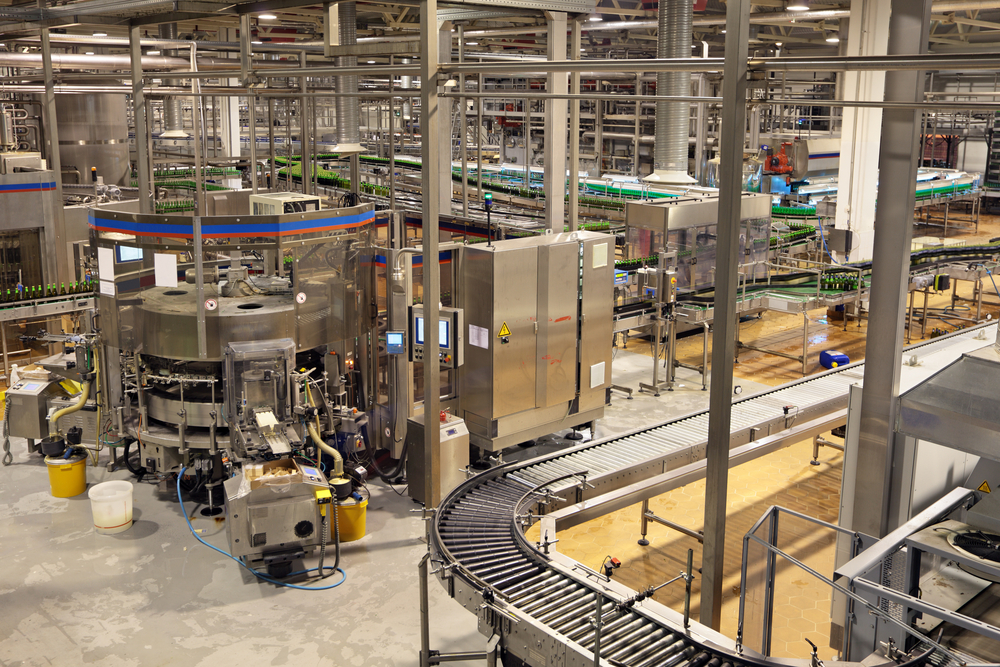
Within the beverage industry, whether it be those brewing beer, wine, spirits, or seltzers, one thing is always assured: rapid change. Technology, trends, and customer tastes are always changing, and any successful brewery must be able to keep pace with the industry as a whole. This is not something that can always be accomplished alone, and that is where Actemium comes in. For breweries looking to solve a variety of problems they might be facing, while also streamlining operations and production schedules, a process engineering consultancy can help immensely.
For any brewery with a new project in mind, whether it’s upgrading their facility in general, or brewing a brand-new beverage, it is crucial that the project is managed correctly to avoid overspending, delays, and quality control issues. It can be difficult to run a brewery and manage its growth all at the same time, so this is where consultancy firms usually enter the picture. In most cases, project management is a part of a larger process engineering consultation, as a natural accompaniment towards the latter half of a project.
How consultancy firms work with their clients
More often than not, Actemium works closely with our client’s own technical teams to develop the perfect, unique solution for their situation. Once a solution has been designed and approved by the client, then we can get to work. Actemium has decades of experience when it comes to procurement and development, and we are always prepared to function as construction and project managers on behalf of the client so they can achieve the results they’ve been dreaming of. The best process engineering consultancies function as an extension of the client, making decisions in their best interest and achieving high quality solutions.
Working with Actemium, instead of a brewery doing all the work themselves, provides numerous benefits. Primarily, there is a massive difference in terms of expertise and experience, as seasoned process engineering consultancies have dealt with many clients over a large span of time, affording them unparalleled proficiency as they tackle all aspects of brewery upgrades or expansions. In relation to this wealth of knowledge exists a wealth of connections, which top process engineering consultancies have cultivated through decades of operation that can be leveraged to secure equipment quickly and, sometimes, more affordably. Process engineering consultancies thus offer convenience to the client, handling design, planning, purchasing, installation, and so on.
What parts of project management are relevant to breweries?
We think one of, if not the most important aspects of brewery project management is tank utilization. Tanks are expensive and can be large and cumbersome to transport and install, so ensuring that the optimal number of tanks are present and properly utilized is key when it comes to engineering an efficient brewery process. A brewery with too many tanks may outpace its packaging capabilities, leading to wasted product, or it could have too little tank storage and fail to meet a desired level of output, leading to lowered revenue.
All types of tanks, from bright or fermenting, to aging tanks can be utilized incorrectly or inefficiently if not properly considered during the design and engineering stages of a project’s lifespan, potentially leading to wasted product. Since product can only be stored in a bright tank for a certain amount of time before needing to be packaged, planning the scheduling and capacity of the process as a whole is critical. Losing product because it cannot be processed fast enough at the final hurdle of packaging is unacceptable. Simple as that. Process engineering consultancy firms are well equipped to calculate and implement these calculations and balances into the design of a brewery, and properly manage a brewery’s resources to minimize waste and inefficiencies.
A final consideration related to tank capacity and utilization is a brewery’s filtration capacity. These can be similarly expensive to tanks and can cause bottlenecks which could drastically impact production. Understanding the ratio between tank capacity, filtration capacity, and packaging capacity is essential for any brewery, and process engineering consultancies are well-equipped to identify shortfalls and run calculations in the name of designing the best solution for any facility.
It’s not just about capacity, let’s talk licensing, regulations, and safety
You know it, but we’ll say it again: anything related to food and beverage comes with seemingly endless regulations and safety procedures attached to ensure only high-quality products make it to store shelves. Proper sanitation procedures and clean in place (CIP) capabilities are crucial to a facility running smoothly and above code. Breweries, somewhat uniquely, deal extensively with yeast and bacteria in their production processes and must be especially careful to ensure that no pathogens or bacteria are present in the final product shipped to customers.
In pursuit of cleanliness and bacteria-free production equipment and environments, special care must be taken for all pipes and welds. Obviously, breweries rely heavily on both, as they transport materials between stages of production and various vessels, skids, tanks, and filling equipment. Within any brewery, there will be all manner of pipes situated in different orientations and slopes, and poor design or planning can lead to “dead legs”, where liquids pool in parts of piping and sit for extended periods of time, running the risk of bacteria buildup. If this is overlooked during design and implementation, it may not become apparent immediately, leading to complications in the future where a brewery is frantically searching for the source of bacteria in their final product. Welds must also be sanitary and quality welds, with external and internal inspections completed to verify cleanliness.
For new products or processes, multiple inspections, certifications, and regulations are needed before anything can be pushed to market. For example, a brewery aiming to transition to seltzer production will appreciate the assistance of process engineering consultancy firms, who know the ins and outs of regulations through countless client experiences. Consultancy firms can guide clients through application processes and help them get started on the right path to properly certified and approved facilities. Within Canada specifically, there exists a CRN (Canadian Registration Number) system which reviews, and registers designs for pressurized equipment, and a governing body must approve initial designs, field-testable solutions, and the finished product before projects can be finalized. Additionally, there are regulations related to taxation when it comes to the production of various alcoholic beverages, with certain licenses needed for certain types of drinks. Process engineering consultancies have more than enough experience to assist the client and guide them through what licenses and certifications are needed for operation, as well as helping them get started on the application process.
Consultancies can help train workers as well
New systems are often different enough from previous iterations to warrant fresh training programs for employees. Actemium works closely with OEMs of specific equipment within a system come in and offer training to our clients, and also offers extensive instruction related to systems we build ourselves. Sometimes both are necessary, depending on the nature of the project, but breweries can rest assured that their partnered firm is ready to teach them everything they need to know to get the most out of their equipment and staff.
Asset care is also something that we can handle. Documentation such as SOPs, FMEAs, LOTOTO, CILs, maintenance programs and spare parts analysis are provided to the client, in addition to functional descriptions of equipment for the purposes of end user education.
Into the future
Revitalizing current systems or building new ones is not all we do for our clients. Right now, a big topic is the use of plastics in manufacturing, as the Canadian government has introduced legislation which will ban the manufacturing, import, and sale of single-use plastics by 2023. This will have a significant impact on the packaging aspect of breweries specifically, as plastic ring carriers have been a common aspect of multi-pack beverages for some time.
Reducing CO2 usage is also a common effort made by many process engineering consultancies, as they strive to reduce carbon dioxide emissions by replacing its use with nitrogen or other gasses. As in other industries, automation through the use of robotics is an emerging area in brewery project management. Labour intensive processes can be streamlined through advanced robots, allowing tighter and leaner scheduling for facilities.
When in doubt, reach out! We at Actemium are ready to assist with project management and beyond, so chances are if you’ve got a problem, we have experts ready to find opportunities for your company to grow as a result of them.